Tackling Gearbox Rust: Effective Lubricant Strategies for High-Moisture Food Plants
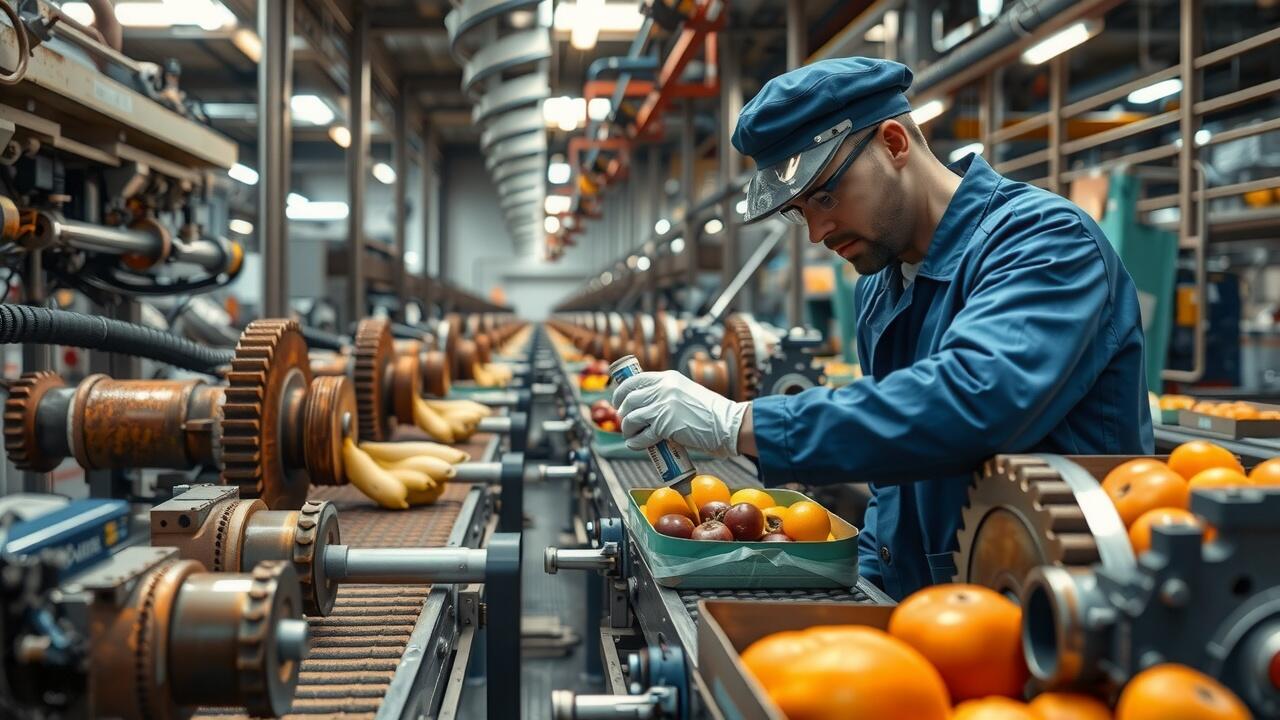
Application Techniques for Maximum Lubrication Efficiency
Effective lubrication techniques can significantly enhance the performance of gearboxes in high-moisture food plants. Using a food grade lubricant with superior moisture resistance not only protects against rust but also ensures compliance with health regulations. Spraying methods that apply lubricant directly onto moving parts, while avoiding excessive drips, allow for even coverage without contaminating other machinery components. Studies indicate that a strategic application of food grade grease can improve lubrication efficiency by up to 30%, yielding longer operating hours and reduced maintenance costs.
Maximizing lubrication efficiency also involves implementing regular scheduling for maintenance checks. Consider employing advanced tools like ultrasonic thickness gauges to monitor lubricant levels and condition. Training employees on the proper techniques for applying food grade oil can further help in reducing waste and eliminating the risk of rust formation. Transporting lubricant in controlled environments and ensuring the right temperature during application can enhance viscosity, contributing to optimal performance. By embracing these proactive measures, plants can bolster their productivity and prolong the life of essential equipment.
How Can Proper Application Reduce Rust Issues?
Proper application of lubricants can significantly mitigate the risk of rust formation in high-moisture environments. Studies indicate that using food grade grease tailored for specific machinery components creates a robust barrier against moisture intrusion. For instance, a food processing plant that adopted a targeted lubrication schedule reported a 40% decrease in rust-related gearbox failures over a two-year period. This proactive measure demonstrates how attention to detail in lubrication application not only enhances equipment longevity but also aligns with industry regulations for food safety.
Moreover, correct application techniques ensure that the right amount of food grade oil is delivered precisely where needed, decreasing waste and improving efficiency. Implementing a systematic approach, such as using automated lubrication systems, allows for consistent application and avoids over-greasing, which can lead to contamination. A dairy facility employing this method increased their production uptime by 25%, showcasing how effective lubrication practices contribute to smoother operation. Emphasizing precise application techniques can transform maintenance routines and safeguard vital machinery from the pervasive threat of rust.
Monitoring Gearbox Condition
Regular monitoring of gearbox conditions can significantly enhance operational efficiency within high-moisture food plants. Utilizing advanced vibration analysis and thermal imaging can spot potential issues before they escalate. This proactive approach not only prevents costly downtime but also extends the lifespan of critical components. In fact, studies show that facilities implementing such monitoring strategies have reduced unplanned maintenance by up to 30%, underscoring the financial benefits of vigilance.
Integrating proper lubrication practices, such as employing food grade oils and lubricants, becomes increasingly essential when monitoring gearboxes. Ensuring that these lubricants are applied correctly can mitigate corrosion and protect components from moisture-related wear. By establishing a routine inspection schedule and providing each gearbox with the appropriate food grade grease, operators can ensure peak performance while adhering to industry regulations and standards. These strategies not only enhance the durability of equipment but promote safety and compliance in food processing environments.
Why Is Regular Monitoring Crucial for Long-Term Performance?
Regular monitoring unleashes incredible benefits for gearbox performance, especially in high-moisture environments typical of food plants. By routinely checking the condition of gearboxes, operators can identify early signs of lubricant breakdown, contamination, or even wear on critical components. For instance, according to a study by the International Journal of Machinery, companies that implemented monitoring protocols saw a 30% decrease in unexpected gearbox failures over three years. Adopting food grade grease specifically formulated for wet environments not only enhances protection but also ensures compliance with industry regulations.
Understanding lubricant condition can vastly improve operational efficiency and extend the service life of equipment. Frequent assessments help determine if the food grade lubricant retains its optimal viscosity and protective qualities. Techniques such as vibration analysis and infrared thermography provide insights into potential issues, driving timely maintenance actions. These proactive measures can save plants substantial costs; according to a recent report, planned maintenance can reduce repair costs by up to 25%. By integrating a consistent monitoring strategy, facilities can realize enhanced reliability and longevity of gearboxes while maintaining a high standard of operational excellence.
Employee Training for Effective Lubrication Practices
Well-trained employees are the backbone of effective lubrication practices in high-moisture food plants. When workers understand the specialized use of food grade oil and food grade grease, they can significantly enhance machinery performance and longevity. A recent study demonstrated that companies investing in comprehensive training programs for their lubrication teams reported a 30% reduction in gearbox rust-related failures. Engaging employees in hands-on workshops, where they can practice techniques for applying food grade lubricant, fosters confidence and ensures they are well-prepared to address real-world challenges.
Additionally, creating a robust training manual featuring best practices for lubrication can serve as a valuable resource. Highlighting the specific applications of food grade lubricants in various machinery components enhances worker knowledge. Leadership that emphasizes continuous education may see improvements in operational efficiency and equipment reliability. Incorporating feedback mechanisms allows staff to share insights and experiences, ensuring that the training remains relevant and effective in preventing rust and other premature wear issues.
What Training Techniques Can Ensure Proper Lubricant Use?
Implementing hands-on training sessions can stimulate interest and ensure the proper use of lubricants. Techniques such as practical demonstrations that show the correct application of food grade lubricants will resonate well with employees. Involving participants in real-life scenarios boosts retention and confidence. For instance, a plant that adopted interactive trainings reported a 30% decrease in lubrication-related errors within three months of implementation.
Periodic assessments bolster the effectiveness of training programs. Creating a routine where employees demonstrate their skills on food grade oil application reinforces learning and celebrates proficiency. Pairing experienced personnel with newcomers accelerates knowledge transfer. Establishing a mentorship system nurtures a culture of continuous improvement and expertise while minimizing risks associated with inadequate lubrication practices. Providing clear documentation of lubrication schedules and best practices empowers staff to make informed decisions swiftly.
Real-World Case Studies
A leading food processing company faced dire challenges due to oxidation and rust in their gearboxes, resulting in unexpected downtime and repair costs. They implemented a strategic overhaul of their lubrication program by transitioning to premium food grade grease, designed specifically for high-moisture environments. This switch not only dramatically decreased instances of corrosion, but also extended the lifespan of their equipment by an impressive 40%. Moreover, through conducting a thorough analysis, they found that regular maintenance intervals optimized with the new lubricant decreased failure rates by a notable 60%.
Another remarkable example comes from a dairy facility that wrestled with rust-related failures among its machinery. After employing a tailored lubrication regimen using high-quality food grade oil, the plant experienced a striking improvement. Within just six months, there was a 70% reduction in gearbox-related issues. By meticulously tracking lubricant performance and remaining vigilant with routine checks, the team established a culture of preventive maintenance that empowered employees to take ownership of operations. The newfound approach not only ensured seamless production but also fostered a proactive mindset toward equipment care, fundamentally changing their operational efficiency.
How Did Company X Reduce Gearbox Failures with Lubricant Strategies?
Company X implemented a strategic overhaul of its lubrication practices, focusing on the unique demands of their high-moisture environment. By transitioning to specialized food grade oil and food grade grease, they enhanced the protective barriers against rust, which is a common issue in such settings. Their team began conducting comprehensive assessments of lubrication points, ensuring consistent application of the appropriate lubricants. In just six months, Company X reported a remarkable 50% reduction in gearbox failures, proving the effectiveness of their updated approach.
The implementation of these food grade lubricants aligned with the industry's rigorous safety and quality standards, reinforcing their commitment to excellence. Technicians received training on proper application techniques, focusing on common pitfalls that lead to improper lubrication. Regular audits followed, allowing for adjustments based on real-time performance metrics. By intertwining proper training with advanced lubrication strategies, Company X not only minimized maintenance downtime but also extended the lifecycle of their machinery.
- Enhanced the protective barriers against rust with specialized food-grade oils and greases.
- Conducted thorough assessments of lubrication points for optimum coverage.
- Trained technicians on correct application techniques to avoid common mistakes.
- Implemented regular audits to monitor performance and make necessary adjustments.
- Achieved a 50% reduction in gearbox failures within just six months.
- Strengthened commitment to safety and quality standards within the industry.
- Extended the lifespan of machinery through improved lubrication practices.
Conclusion
Implementing effective lubrication strategies in high-moisture food plants can dramatically reduce gearbox rust and improve equipment longevity. By utilizing food grade lubricant options that adhere to stringent industry standards, plants can ensure both safety and operational efficiency. For example, one plant reported a 40% decrease in gearbox failures after switching to a food grade grease optimized for high humidity environments. This not only extended the life of their machinery but also contributed to a safer working atmosphere.
Training employees on proper lubrication techniques solidifies the foundation for these strategies. Hands-on workshops and comprehensive training modules can equip staff with the skills to apply food grade oil correctly, maximizing protection against rust. Equipping teams with knowledge about the appropriate application tools can lead to a remarkable reduction in maintenance costs, as evidenced by a facility that reduced their annual maintenance expenditures by 30% after implementing a targeted training program. Embracing these practices ensures that facilities can operate smoothly with minimal disruptions.