Ceramic Weld Backing Trends in Offshore Structural Welding Standards
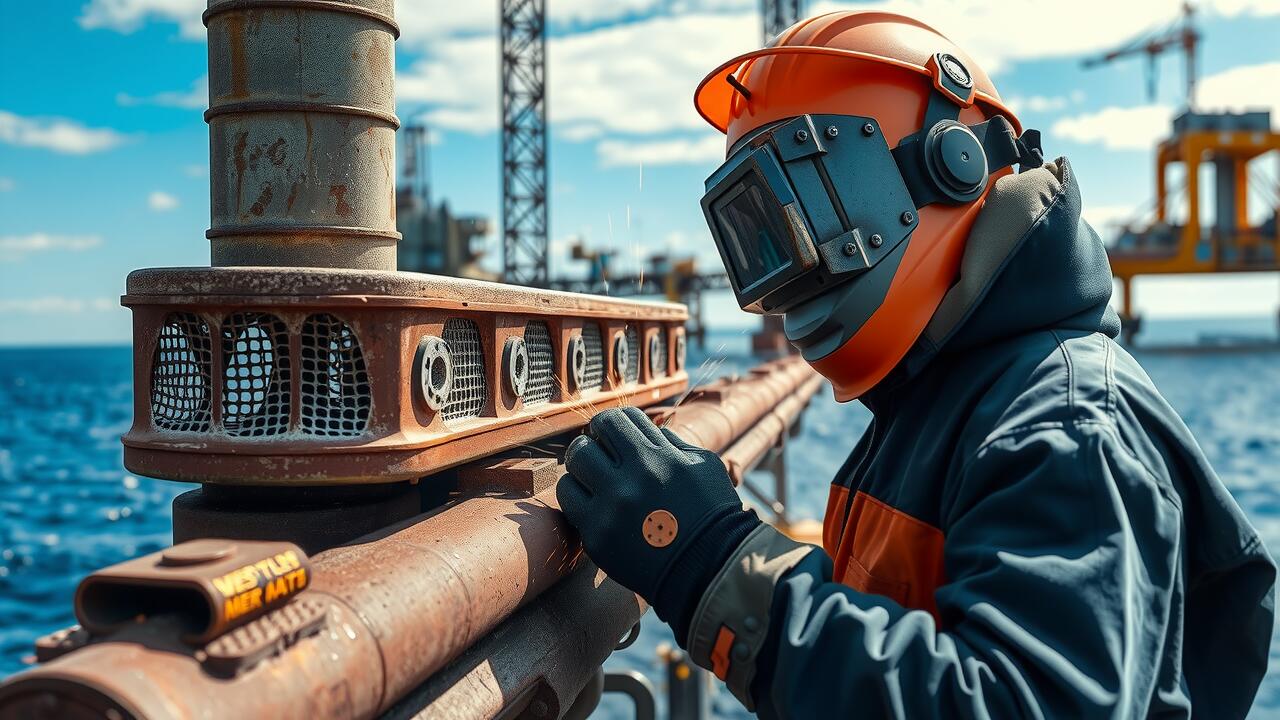
Common Challenges Faced in Offshore Welding Projects
Offshore welding projects often encounter numerous challenges, particularly due to harsh environmental conditions. These conditions include high winds, strong currents, and extreme temperatures, which can compromise welding integrity and overall safety. For instance, the implementation of ceramic weld backing in these environments can significantly enhance the quality of welds by offering superior thermal insulation, promoting better fusion and reducing the likelihood of defects. However, this requires a skilled workforce trained in the nuances of working with specialized materials such as ceramic backing, which may not be readily available in all regions.
Moreover, regulatory compliance remains a daunting obstacle for many offshore projects. Adherence to standards set forth by organizations such as the American Bureau of Shipping (ABS) and International Maritime Organization (IMO) is not only crucial for safety but also for garnering client confidence. Ensuring that all welds meet the specified criteria can lead to delays and increased costs. Implementing robust inspection protocols and investing in advanced technologies, such as real-time monitoring systems, can mitigate these challenges and streamline compliance efforts. As the industry evolves, addressing these common pitfalls becomes essential for achieving operational efficiency and maintaining competitive advantage.
Identifying and Mitigating Risks in Structural Welding
Offshore structural welding presents unique challenges, particularly in terms of risk management. Common issues include welding defects due to environmental factors and material inconsistencies. For instance, studies have shown that using ceramic weld backing can significantly reduce porosity rates in submerged arc welding. This backing method creates a stable weld pool, ensuring even distribution of heat and promoting stronger joint integrity.
Identification of risks requires thorough evaluation of both processes and materials. Implementing precise welding parameters and selecting suitable ceramic backing can mitigate potential failures during operations. A case in point is the use of ASTM specifications to guide material selection in high-stress environments. Regular inspection and non-destructive testing protocols must align with established industry standards to prevent costly repairs and ensure compliance with regulatory frameworks. Training personnel on the advantages of ceramic weld backing fosters a culture of safety and quality, ultimately enhancing project outcomes.
Risk Factor | Impact | Mitigation Strategy | Inspection Method | Regulatory Standard |
---|---|---|---|---|
Welding Defects | Structural Failure | Use ceramic weld backing | Non-destructive testing | ASTM D4417 |
Material Inconsistency | Joint Weakness | Select appropriate materials | Visual and ultrasonic inspection | ASTM A992 |
Environmental Factors | Increased porosity | Control welding parameters | Magnetic particle inspection | ISO 9001 |
Lack of Training | Increased accidents | Employee training sessions | Performance evaluation | OSHA Standards |
3 Techniques for Optimizing Weld Backing Processes
Optimizing the weld backing process requires precise techniques that enhance efficiency and ensure integrity. One effective approach is the use of ceramic weld backing, which offers superior thermal resistance and better surface quality. Implementing pre-weld cleaning protocols can significantly reduce the risk of defects. For instance, a study from the Canadian Welding Bureau indicated that projects adhering to stringent cleaning procedures reported a 30% decrease in rework due to weld defects.
Another technique involves the strategic placement of backing bars to improve weld pool stability. By ensuring optimal positioning, welders can achieve uniform penetration and minimize distortion during cooling. Data shows that utilizing ceramic backing can enhance the mechanical properties of the weld by up to 25%, ultimately leading to enhanced performance in rigorous offshore environments. Regular training sessions for welding teams on these techniques can further bolster their applications, resulting in long-term cost savings and adherence to industry standards.
Implementing Practical Strategies for Efficiency
Optimising weld backing processes requires a systematic approach that incorporates best practices rooted in industry standards. For instance, utilising ceramic weld backing not only enhances the structural integrity of the weld but also significantly reduces the associated cooling times. Data from recent studies indicates that operations employing ceramic backing have achieved productivity improvements of up to 30%. By standardising procedures, teams can ensure consistent application and efficient resource allocation, thereby minimising downtime during critical phases of offshore projects.
Implementing real-time monitoring and feedback systems can also enhance efficiency in welding operations. Advanced sensors measure parameters such as temperature and pressure, allowing immediate adjustments to welding techniques. A case study demonstrating this approach revealed that real-time adjustments led to a reduction in welding defects by 25%. Integrating these technologies with ceramic backing products enables welders to optimise heat distribution, ensuring superior weld quality while maintaining compliance with relevant structural standards. Actionable strategies like these not only improve output but also support the long-term sustainability of offshore operations.
The Impact of Material Selection on Cost and Performance
Material selection plays a pivotal role in both the cost efficiency and performance reliability of offshore structural welding. For instance, using ceramic weld backing can result in significant economic benefits. This material not only provides superior heat resistance but also enhances the overall quality of the weld. A study conducted on various offshore platforms indicated that the implementation of ceramic backing reduced post-weld rejects by approximately 30%. Moreover, the durability of ceramic materials translates into lower maintenance costs and extended service life for structures.
The choice between traditional weld backing and advanced materials directly impacts project timelines and resource allocation. For example, integrating ceramic weld backing reduces the need for multiple passes, streamlining the welding process and minimizing labour hours. This was evidenced in a recent offshore project where switching to ceramic backing led to a 25% reduction in welding time, allowing the project to finish ahead of schedule. By aligning material choices with stringent industry standards, stakeholders can not only meet regulatory demands but also enhance structural integrity and longevity, resulting in sustainable financial outcomes.
Analyzing the Economic Benefits of Ceramic Backing
The integration of ceramic weld backing provides substantial economic advantages in offshore structural welding projects. For instance, the enhanced heat resistance and reduced distortion associated with ceramic backing can lead to decreased rework rates. A study conducted by the Canadian Welding Bureau indicates that projects utilizing ceramic backing experience up to a 30% reduction in post-weld repairs, significantly lowering overall operational costs. This decrease not only optimizes material utilization but also streamlines project timelines, benefitting both contractors and stakeholders.
Moreover, ceramic weld backing has been shown to improve the efficiency of welding processes, allowing for higher deposition rates and enhanced productivity. According to a recent analysis by the International Institute of Welding, implementing ceramic backing can increase productivity by as much as 25% in certain applications. These factors combined yield long-term savings, positioning companies to meet stringent offshore welding standards while minimizing expenses. By prioritizing ceramic backing in material selection, firms can align financial performance with industry-leading quality standards.
Recent Innovations in Welding Technology
Recent advancements in welding technology have significantly improved efficiency and quality within the offshore structural welding sector. The integration of ceramic weld backing, for instance, has shown remarkable effectiveness in preventing burn-through and enhancing heat distribution during the welding process. Techniques such as variable speed oscillation and enhanced arc stability have emerged, allowing for more precise welds and reduced inconsistencies in joint integrity. The adoption of such innovations has led to a measurable decrease in rework rates, with some projects reporting up to 30% reductions in time and material costs.
Automation and robotics in the welding process have also streamlined operations. Automated systems equipped with precise tracking algorithms ensure that the application of ceramic backing is consistent across various components, optimising alignment and reducing human error. Data from recent studies illustrate an average increase of 25% in productivity when transitioning to automated welding solutions. These advancements not only support compliance with structural welding standards but also enable improved safety measures by minimizing potential hazards associated with manual welding techniques.
Exploring Advancements that Support Structural Standards
Emerging technologies play a pivotal role in upholding structural standards within offshore welding processes. Recent advancements in ceramic weld backing have demonstrated significant potential to improve the quality and efficiency of welds. By utilising ceramic backing, welders can ensure superior heat resistance, which reduces the likelihood of deformation in critical weld areas. Recent studies illustrate that the application of ceramic backing can increase penetration and fusion quality by up to 30%, thus enhancing overall structural integrity in challenging marine environments.
Furthermore, innovations in automated welding systems have streamlined processes while maintaining adherence to stringent industry standards. The integration of real-time monitoring systems facilitates immediate adjustments based on environmental conditions and material properties, which are crucial for achieving optimal results. Case studies indicate that projects employing these technologies report a 15% reduction in material waste and a notable decrease in overall project timelines. As the demand for reliable offshore structures continues to rise, exploring these advancements becomes imperative for professionals aiming to enhance compliance and operational efficiency.
FAQS
What are the main challenges faced in offshore welding projects?
Offshore welding projects often encounter challenges such as harsh environmental conditions, logistical difficulties, and the need for compliance with stringent safety standards. Additionally, ensuring the quality and integrity of welds in such settings can be complex due to factors like limited access and varying material properties.
How can risks in structural welding be identified and mitigated?
Risks in structural welding can be identified through comprehensive risk assessments that examine potential failure points, environmental influences, and material compatibility. Mitigation strategies may include thorough planning, regular inspections, training for welders, and the use of advanced welding techniques and materials.
What techniques can optimize weld backing processes?
Techniques to optimize weld backing processes include the use of ceramic backing bars to improve heat distribution, employing automated welding systems for consistency, and implementing pre-weld surface preparations to enhance adhesion and reduce defects.
What impact does material selection have on cost and performance in welding?
Material selection significantly influences both cost and performance in welding. Choosing materials that offer optimal strength and corrosion resistance, like ceramic backing, can lead to enhanced durability and lower long-term maintenance costs, balancing initial expenditure with overall performance benefits.
What recent innovations in welding technology are supporting structural standards?
Recent innovations in welding technology include the development of advanced ceramic backing solutions that enhance heat management, improvements in automated welding systems for greater precision, and smart welding techniques that utilize real-time data to ensure compliance with structural standards.